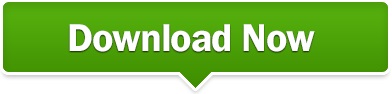


In computational weld mechanics (CWM), the thermal load is obtained by using power density distribution functions that calibrate parameters using experimental results.
#Ansys 2015 for mac free#
Weldments free from defects and stresses within the yield limits of the base materials were obtained. In subsequent work, they deepened the weldability of such similar and dissimilar welded joints. It was concluded that the pulsed current-induced low residual stresses in the weld region were within the factor of safety of parent materials. Two levels of each welding factor, filler wire and root gap parameters, were chosen for the experiments. The L 4 orthogonal array was chosen for the tests. studied the residual stress evolutions in multi-pass dissimilar joints (IN 625-AISI 316L). Finally, the influence of the 3D model size on the temperature, residual stress, and displacement distributions was investigated. Results of thermal and displacement distributions were found in good agreement with those measured in real joints. proposed a T-joint numerical model conducted by combining the shell and 3D finite elements. In order to decrease the computational time without losing accuracy, Perić et al. In this case, despite the fact that defect-free welded joints were obtained, failures occurred at the weld region and the average tensile strength of the weldments was found to be 852.4 MPa. investigated the weldability and metallurgical and mechanical properties of the PCGTA welded Inconel 625 alloy employing ERNiCrMo-3 filler wire. Tensile tests showed that the failure occurred within the parent metal, proving the high quality and strength of the welded joints obtained. The ERNiCrMo-3 alloy was used as filler wire. In another recent work, Balram and Rajalakshmi reported the experimental results regarding thermal stresses and thermal fields developed in the GTAW process applied to similar and dissimilar welded joints. However, the authors did not focus on residual stresses caused by the joining process. Temperature results obtained by using volumetric heat source were in good agreement with those obtained employing thermocouples located at the heat-affected zone of the joints. developed an FEA model for multi-pass GTAW process of Incoloy 800 pipes. Experimental tests can be performed to estimate the improvement in parameters, but they are expensive and also quite time-consuming in this scenario, welding numerical simulation may help avoid such drawbacks. Further, these welding process parameters will affect structural integrity.

The selection of welding process parameters is one of the major challenging tasks to control welding residual stresses and distortions. In particular, gas tungsten arc welding (GTAW) allows yielding sound welds with different alloys. Introductionįusion welding is one of the major joining techniques employed in industrial applications. The agreement between the measured and analysed residual stress was 11%. Thermal measurements were collected pass by pass from the analysis, and the agreement was 9.08%.

Simulations were performed with ANSYS numerical code, and a close agreement was found between the predicted and experimentally measured residual stress. X-ray diffraction techniques were used to measure residual stresses, and IR thermometry was employed to capture the temperature values on the welded joints. Experiments were carried out with 5 mm thick Inconel 625 plates. Thermomechanical analysis is carried out to assess the Thermal and residual stress distributions. A multi-pass welding model was developed that uses a volumetric heat source. Thermal and residual stress distributions induced by the gas tungsten arc welding (GTAW) process on Inconel 625 were studied using numerical simulation and experiments.
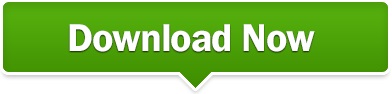